How to Conduct a Thorough Construction Risk Assessment to Prevent Hazards in 5 Steps
Construction sites inherently pose numerous hazards that can result in injuries, property damage, or project delays if not properly identified and managed. Each year, accidents can result in significant injuries, devastating fatalities, and substantial financial burdens, including average medical expenses of $42,000 per injury and workers' compensation claims averaging $41,757.
A thorough risk assessment provides the foundation for a comprehensive safety program by systematically identifying potential dangers before they cause harm. Conducting a proper construction risk assessment not only helps comply with health and safety regulations but also significantly reduces workplace accidents and associated costs.
Risk assessments in construction aren't just bureaucratic exercises but practical tools that save lives and protect investments. When properly implemented, they create a proactive safety culture where potential problems are addressed before becoming incidents. The process requires attention to detail, industry knowledge, and a methodical approach to evaluating each aspect of a construction project for potential risks.
1) Identify Potential Hazards by thoroughly inspecting the entire construction site
The first critical step in any effective construction site risk assessment is conducting a thorough site inspection. This involves systematically walking through the entire construction area to observe ongoing activities, site conditions, and equipment in use.
Look for obvious hazards such as uneven surfaces, sharp edges, exposed wires, or missing guards on machinery. These physical dangers can be immediately apparent during a comprehensive walkthrough of the site.
Pay close attention to work at heights, excavations, electrical systems, and heavy machinery operations. These areas typically present higher risks and require extra scrutiny during the inspection process.
Document all identified hazards using checklists, photographs, or digital tools. This creates a record that can be referenced throughout the project and ensures no potential danger goes unaddressed.
Consider different times of day and varying weather conditions when identifying hazards. Some risks may only become apparent in specific conditions, such as poor visibility at dusk or slippery surfaces after rainfall.
Engage workers in the identification process as they often have firsthand knowledge of hazards in their specific work areas. Their practical insights can reveal issues that might not be immediately obvious to inspectors.
Review project plans and specifications to identify potential design-related hazards before they manifest on site. Proactive identification at this stage can prevent costly modifications later.
The hazard identification process should be systematic and comprehensive, leaving no area of the construction site uninspected. Thoroughness at this stage forms the foundation for all subsequent risk assessment steps.
To empower this identification phase, SafetyVue provides the data-driven foresight needed to move beyond reactive measures. SafetyVue enhances your ability to predict and address potential hazards proactively, ensuring a more secure and efficient job site right from the start.
2) Assess the Risks associated with each identified hazard using qualitative and quantitative methods
After identifying hazards in a construction environment, the next critical step is assessing the risks associated with each hazard. This assessment provides the foundation for implementing appropriate control measures based on the severity and likelihood of potential incidents.
Risk assessment can be approached through two complementary methods: qualitative and quantitative analysis. Both techniques offer valuable insights when determining which risks require immediate attention.
Qualitative risk assessment involves categorizing risks based on their severity and probability using descriptive scales. Construction managers typically use a risk matrix that plots severity (minor to catastrophic) against likelihood (rare to almost certain).
This method is relatively quick to implement and doesn't require extensive historical data. It helps prioritize risks through categories such as low, medium, high, or extreme based on their position in the matrix.
Quantitative risk assessment involves assigning numerical values to both the probability and consequences of identified hazards. This data-driven approach provides more precise measurements of risk levels compared to qualitative methods.
For example, a construction company might calculate that a specific fall hazard has a 5% probability of occurring with potential financial impacts of $250,000, resulting in a quantified risk value of $12,500.
Construction teams should consider factors like worker exposure frequency, proximity to the hazard, and historical incident data when determining risk levels. Environmental conditions and the current state of equipment also significantly influence risk assessment.
Risk assessment should account for both immediate consequences (injuries, property damage) and long-term impacts (chronic health issues, regulatory penalties). This comprehensive view ensures no potential consequences are overlooked.
The risk assessment process becomes more effective when combining qualitative and quantitative methods. Starting with qualitative assessment helps identify priority areas, while follow-up quantitative analysis provides the detailed data needed for resource allocation.
It's essential to involve multiple stakeholders including site supervisors, safety officers, and workers when assessing risks. Their diverse perspectives ensure a more comprehensive understanding of potential hazards and their implications.
Documentation of all risk assessments is crucial for maintaining safety standards and compliance. Detailed records help track risk trends over time and provide evidence of due diligence in maintaining workplace safety.
SafetyVue's digital risk assessment tools help construction teams identify qualitative and quantitative risk evaluations, enabling real-time hazard tracking and providing data-driven insights to enhance overall site safety.
3) Implement Control Measures to eliminate or reduce risks to acceptable levels
After identifying and assessing construction hazards, the next critical step is implementing effective control measures. These measures aim to eliminate risks completely or reduce them to acceptable levels where they no longer pose significant threats to workers.
The hierarchy of controls provides a systematic approach to managing workplace hazards. This framework prioritizes control measures from most to least effective: elimination, substitution, engineering controls, administrative controls, and personal protective equipment.
Elimination is the most effective control measure as it completely removes the hazard. This might involve redesigning the construction process or using alternative building methods that don't require hazardous materials or procedures.
Substitution involves replacing dangerous materials or processes with less hazardous alternatives. For example, using water-based paints instead of solvent-based ones reduces exposure to harmful chemicals.
Engineering controls create physical barriers or modifications to minimize risk. These might include installing guardrails around elevated work areas, using mechanical lifting devices to prevent manual handling injuries, or implementing noise reduction barriers.
Administrative controls change how people work through policies, procedures, and training. This includes implementing permit-to-work systems, conducting regular safety briefings, and developing emergency response procedures.
Personal Protective Equipment (PPE) serves as the last line of defense. While essential, PPE should never be the only control measure implemented. Proper PPE for construction might include hard hats, safety glasses, high-visibility clothing, and respiratory protection.
Control measures should be selected based on the risk assessment findings, prioritizing hazards on a "worst-first" basis when resources are limited. This ensures the most dangerous risks receive immediate attention.
Regular monitoring and review of control measures are essential to ensure their continued effectiveness. Construction environments change rapidly, requiring ongoing assessment of safety protocols.
Documentation of all implemented control measures creates accountability and provides reference for future safety planning. This documentation should detail specific controls, implementation dates, and responsible parties.
Proactive safety management significantly reduces workplace incidents and associated costs. Rather than reacting to accidents, construction companies that anticipate and address potential hazards create safer, more productive work environments.
SafetyVue helps construction companies implement control measures through digital risk assessment tools. The platform enables real-time monitoring of safety protocols, ensuring construction teams can quickly identify and address emerging hazards before they cause harm.
4) Engage Frontline Employees in the risk assessment process for practical insights
Frontline workers possess invaluable knowledge about day-to-day construction operations that can significantly enhance risk assessment effectiveness. Their hands-on experience allows them to identify hazards that might be overlooked by management or safety professionals who aren't regularly on site. These employees witness potential dangers firsthand and understand the practical limitations of certain safety controls.
Creating a collaborative environment where workers feel comfortable sharing observations is essential. Construction companies should establish clear channels for reporting hazards without fear of reprisal. Regular toolbox talks and safety meetings provide excellent opportunities to gather input from those who interact with equipment and materials daily.
Risk assessment should be a collaborative process that includes soliciting input on hazard identification, involving workers in job safety analyses, and getting feedback on control measures. This approach leverages the practical experience of those who perform the work regularly.
When frontline employees participate in risk assessments, they develop a stronger sense of ownership over safety protocols. This engagement leads to better compliance with safety measures because workers understand the reasoning behind them. Their participation also helps ensure that risk controls are practical and won't be circumvented due to inefficiency.
Frontline workers provide critical insights that can significantly enhance the effectiveness of risk identification, assessment, and mitigation strategies. Their practical knowledge often reveals issues that might not be apparent during theoretical risk evaluations conducted away from the worksite.
Construction managers should consider implementing a rotating system where different workers participate in risk assessments. This approach ensures diverse perspectives and helps spread safety awareness throughout the organization. It also demonstrates that management values worker input and takes their concerns seriously.
Engaging employees in the risk assessment process is critical for organizations striving to create a resilient and responsive workplace. In the construction industry, this collaborative approach helps identify risks more comprehensively and develops more effective mitigation strategies.
Construction companies can facilitate engagement through digital tools that allow workers to report hazards easily. Mobile applications enable employees to document concerns with photos and descriptions in real-time, providing valuable data for risk assessments. This technology makes participation more accessible and convenient for busy construction professionals.
By identifying and addressing risks before they cause harm, construction companies protect both their workforce and their bottom line. SafetyVue’s mobile app empowers frontline workers with real-time reporting from the field, allowing them to quickly document hazards, share insights with photos and descriptions, and enhance communication, translating critical input into actionable safety improvements across your site
5) Document All Findings and Control Actions Clearly and Maintain Records for Future Review
Documentation is a critical component of any effective risk assessment process. It creates a formal record of identified hazards, risk evaluations, and control measures implemented on the construction site.
Organizations should establish a systematic approach for documenting risk assessment findings that includes comprehensive records of all activities. This includes initial assessments, subsequent reviews, and updates made over time.
Using standardized templates ensures consistency in formatting, structure, and content across all risk assessment documents. Templates help teams follow the same guidelines and reduce the likelihood of important information being overlooked.
A well-documented risk assessment should clearly identify all hazards discovered during the assessment process. Each hazard should be categorized and described with sufficient detail to understand its nature and potential impact.
The documentation must include thorough risk evaluation results, explaining the likelihood and severity of each identified hazard. This quantification helps prioritize which risks require immediate attention versus those that can be addressed over time.
All selected control measures should be clearly documented, indicating how each hazard will be eliminated or minimized. The documentation should specify whether engineering controls, administrative controls, or personal protective equipment will be used.
Assigning clear roles and responsibilities for implementing control measures is essential. The documentation should identify who is responsible for each action, establishing accountability and ensuring nothing falls through the cracks.
Construction companies must maintain a clear and accessible record of all risk assessment findings. Tools like risk registers help organize this information in a structured manner that can be easily referenced when needed.
Regular reviews of documentation should be scheduled to ensure all control measures remain effective. These reviews provide opportunities to update assessments based on changing conditions or new information.
Photos, videos, and other visual evidence can provide valuable context and should be included in the documentation whenever possible. These visuals help communicate hazards more effectively than written descriptions alone.
If the construction company employs 5 or more people, they are legally required to record significant findings including hazards, who might be harmed, and control measures implemented.
Documentation should be stored securely but remain accessible to relevant team members. Digital document management systems can facilitate easier sharing, updating, and retrieval of important safety information.
Proactive safety management goes beyond mere compliance with documentation requirements. By thoroughly documenting risk assessments, construction companies demonstrate their commitment to creating a safety-focused culture.
SafetyVue provides comprehensive digital tools that document construction risk assessments. Their platform enables teams to create, store, and access all safety documentation from a centralized location.
With SafetyVue's mobile capabilities, construction teams can document hazards and control measures directly from the field, ensuring nothing is forgotten when returning to the office. This real-time documentation improves accuracy and completeness of safety records.
Understanding Construction Risk Assessment
Risk assessment forms the foundation of construction safety programs by systematically identifying potential hazards before they cause harm. This process enables teams to allocate resources effectively and develop appropriate mitigation strategies tailored to specific project needs.
Key Principles of Risk Assessment
A construction risk assessment is a systematic approach to identifying, analyzing, and evaluating potential hazards on a construction site. The process follows several key principles that ensure thoroughness and effectiveness.
Risk assessments must be proactive rather than reactive, identifying hazards before incidents occur. This preventative approach saves both lives and resources.
The assessment should be proportionate to the level of risk involved. High-risk activities require more detailed evaluation and stronger control measures compared to lower-risk tasks.
Effective risk assessments involve collaboration and consultation with workers who have firsthand experience with site conditions and tasks. Their input provides valuable practical insights that might otherwise be overlooked.
Documentation must be clear and accessible to all relevant parties, creating a reference point for safety practices and compliance verification.
Types of Hazards in Construction Projects
Construction sites contain numerous potential hazards that vary by project phase, location, and scope. Understanding these hazard categories helps ensure comprehensive assessment.
Physical hazards include falling objects, working at heights, excavations, and moving equipment. These often pose immediate injury risks and require strict safety protocols.
Chemical hazards arise from exposure to substances like solvents, paints, and dust. Long-term exposure can lead to chronic health issues such as respiratory diseases or chemical burns.
Biological hazards include exposure to mold, bacteria, or contaminated materials, particularly in renovation projects or sewage work.
Ergonomic hazards result from poor body positioning, repetitive movements, or manual handling of heavy materials. These can cause musculoskeletal disorders over time.
Environmental hazards include extreme weather conditions, noise pollution, and vibration from equipment. These factors can exacerbate other risks or create new ones in changing conditions.
Ensuring Compliance and Continuous Improvement
Risk assessment in construction isn't a one-time activity but an ongoing process that must align with regulatory requirements while continuously evolving to address new challenges and hazards.
Legal and Regulatory Considerations
Construction projects must adhere to numerous regulations that vary by location and project type. In the United States, OSHA standards form the regulatory backbone of construction safety, with specific requirements for fall protection, scaffolding, and equipment operation.
Compliance risk assessment should be conducted early to identify potential areas of non-compliance, allowing teams to take proactive measures before problems arise.
Documentation is crucial for demonstrating compliance. Maintain detailed records of all risk assessments, safety training, incident reports, and corrective actions taken.
Consider appointing a compliance officer who stays updated on changing regulations and ensures the project team understands their legal obligations.
Strategies for Ongoing Risk Monitoring
Effective risk management requires continuous improvement through regular reassessment and adaptation. Implement a schedule for periodic risk reviews, especially after significant project changes or milestones.
Utilize digital tools and software that can track risks in real-time and alert managers to emerging issues before they escalate.
Encourage a reporting culture where workers feel comfortable identifying new hazards without fear of reprisal. Anonymous reporting systems can be particularly effective.
Conduct post-incident analyses to understand root causes and prevent recurrence. These learnings should be documented and incorporated into future risk assessments.
Benchmark your risk management practices against industry standards and high-performing companies to identify improvement opportunities.
Want to enhance your risk assessment process?
Download "Proactive Safety Strategies: Leveraging Data for Injury Prevention in Construction" for a detailed approach to proactive risk management.
FAQS
What is the most significant cost associated with construction accidents?
What is the most significant cost associated with construction accidents?
What is the most significant cost associated with construction accidents?
What is the most significant cost associated with construction accidents?
What is the most significant cost associated with construction accidents?
Tim Wolter
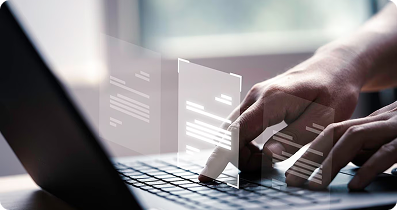