9 Effective Strategies to Prevent Accidents on Construction Sites
Construction sites are inherently dangerous environments where accidents can lead to serious injuries or even fatalities. The combination of heavy machinery, elevated work areas, and constantly changing conditions creates numerous hazards that require vigilant attention and proactive management to ensure worker safety.
Implementing comprehensive safety protocols is the cornerstone of accident prevention in construction environments, reducing incident rates by up to 85% when properly executed. Safety isn't merely about compliance with regulations—it's about creating a culture where everyone takes responsibility for identifying and mitigating risks before they result in harm. Effective strategies focus on both systemic approaches and individual awareness to create truly safe construction environments.
1) Implement Comprehensive Safety Training Programs
Safety training forms the foundation of accident prevention on construction sites. Regular training sessions ensure all workers understand potential hazards and proper safety protocols specific to their roles and responsibilities.
Training programs should cover equipment operation, fall protection, hazard recognition, and emergency procedures. These sessions must be updated regularly to reflect current industry standards and regulations.
New employees should receive thorough orientation training before beginning work. This initial training establishes safety expectations and provides critical knowledge about site-specific hazards.
Refresher courses help maintain awareness and reinforce safety practices among experienced workers. Even veterans in the field benefit from periodic updates on evolving safety standards and technologies.
Documentation of all training activities creates accountability and helps track compliance. Records should include attendance, topics covered, and competency assessments.
Interactive training methods like simulations and hands-on exercises prove more effective than lectures alone. These approaches help workers retain information and apply safety concepts in real-world situations.
2) Enforce Proper Use of Personal Protective Equipment (PPE)
Construction site accidents frequently occur when workers fail to use personal protective equipment correctly. Hard hats, safety glasses, gloves, high-visibility clothing, and steel-toed boots serve as critical barriers between workers and potential hazards.
Site managers must establish clear PPE requirements for different areas and tasks. Regular inspections ensure compliance and identify equipment that needs replacement due to wear or damage.
Training programs should demonstrate proper fitting techniques and explain the protection each piece provides. Workers need to understand why specific PPE is necessary for their tasks rather than viewing it as optional or merely procedural.
Companies that consistently enforce PPE standards see measurable decreases in workplace injuries.
Equipment maintenance schedules are equally important to enforcement. Even the highest-quality protective gear loses effectiveness when damaged or improperly stored.
Creating a culture where workers hold each other accountable for PPE usage strengthens site-wide safety. When proper equipment use becomes habitual rather than enforced, accident rates typically decline substantially.
3) Conduct Regular Site Safety Inspections
Regular safety inspections are crucial for identifying and addressing potential hazards before they cause accidents. These inspections should be scheduled frequently and conducted by qualified personnel who understand construction safety regulations and standards.
Safety inspections should follow a comprehensive checklist that covers all aspects of the worksite, including equipment condition, structural integrity, and proper use of safety gear. Documentation of all findings creates accountability and provides a reference for tracking safety improvements over time.
Unannounced inspections can be particularly effective in revealing everyday practices that might not be visible during scheduled reviews. They offer a more accurate picture of typical safety compliance and worker behavior under normal conditions.
Construction managers should encourage worker participation in the inspection process. Employees often notice hazards that supervisors might miss since they interact with specific equipment and areas daily.
4) Utilize Fall Protection Systems like Guardrails and Harnesses
Falls remain the leading cause of fatalities in construction, making fall protection systems essential on every job site. Properly installed guardrails provide a physical barrier that prevents workers from falling from heights and should be installed around all elevated work areas.
Personal fall arrest systems, including full-body harnesses and lanyards, serve as a critical secondary protection measure. These systems must be inspected before each use to ensure they're free from damage and will function correctly when needed.
Safety nets can be installed to catch workers who may fall when working at significant heights. They provide an additional layer of protection when guardrails alone may not be sufficient.
Hole covers must be secured and labeled to prevent workers from falling through floor openings. Any cover should be able to support twice the weight of workers and equipment that might be placed on it.
Regular training ensures workers understand how to properly wear, inspect, and use fall protection equipment. Construction companies should document all fall protection training and conduct refresher courses annually.
5) Establish Clear Communication Protocols with Radios and Signals
Clear communication is essential on construction sites where noise and distance can create dangerous misunderstandings. Construction teams should implement standardized radio protocols with dedicated channels for different work areas or functions.
Hand signals provide an effective backup when verbal communication isn't possible. All workers must be trained to recognize and use the same set of signals for crane operations, vehicle movements, and emergency situations.
Daily briefings should review communication expectations and remind workers about proper radio etiquette. This includes using clear terminology, confirming receipt of important messages, and avoiding unnecessary chatter that might block critical safety information.
Communication equipment must be regularly tested and maintained. Dead batteries or malfunctioning radios can create dangerous situations when warnings cannot be transmitted quickly.
Construction managers should consider implementing advanced communication technologies like, which can integrate radio communications with visual alerts for workers in high-noise environments. These systems help ensure that critical safety messages reach all team members regardless of environmental conditions.
6) Maintain Proper Equipment Maintenance and Checks
Regular equipment maintenance plays a crucial role in preventing construction site accidents. Faulty machinery or tools can malfunction unexpectedly, creating dangerous situations for workers. Implementing a comprehensive maintenance schedule helps identify potential problems before they cause injuries.
Daily equipment inspections should be conducted before operation begins. These checks ensure that all safety features are functioning properly and that no visible damage exists that could compromise performance or safety.
Detailed maintenance logs should be kept for all equipment, documenting service dates, repairs, and inspections. This documentation provides accountability and creates a reliable history of each piece of equipment's condition and maintenance needs.
Training operators to recognize warning signs of equipment failure is equally important. Workers should know when to report concerns and when to stop using potentially dangerous machinery.
Digital maintenance tracking systems can streamline this process, sending automatic alerts when inspections are due. These systems help construction managers ensure no maintenance checks are missed, even across large projects with numerous pieces of equipment.
7) Create and Enforce Hazardous Material Handling Procedures
Construction sites frequently contain various hazardous materials that pose serious risks to worker safety. Establishing clear procedures for handling these materials is essential for preventing accidents and maintaining compliance with safety regulations.
Proper labeling of all hazardous substances should be mandatory, with Safety Data Sheets (SDS) readily accessible to all workers. Training programs must ensure that every employee understands the risks associated with each material and knows the correct handling techniques.
Personal protective equipment appropriate for specific hazardous materials should be provided and its use strictly enforced. Regular inspections of storage areas help prevent leaks, spills, or improper storage that could lead to accidents.
Emergency response protocols for chemical spills or exposures need to be clearly defined and practiced regularly. To minimize exposure risks, designated storage areas should be properly ventilated and kept away from high-traffic zones.
Documentation of all hazardous material handling procedures creates accountability and helps identify areas for improvement.
8) Install Adequate Lighting in All Work Areas
Poor visibility on construction sites significantly increases accident risks. Workers need to clearly see potential hazards, equipment, and materials to navigate safely through the workspace.
Proper lighting must be installed in all work areas, including enclosed spaces, stairwells, and temporary structures. Construction sites operating during early morning, evening hours, or in locations with limited natural light require special attention to lighting requirements.
Portable lighting solutions offer flexibility for changing workspaces. LED lights are particularly effective due to their energy efficiency, brightness, and durability in construction environments.
Regular maintenance of lighting systems prevents unexpected darkening of work areas. Burned-out bulbs should be promptly replaced, and lighting fixtures must be kept clean from dust and debris that might diminish illumination.
Emergency lighting systems should be installed and regularly tested. These backup systems ensure workers can safely evacuate during power outages or other emergencies.
9) Develop Emergency Response and Evacuation Plans
Even with rigorous safety protocols, emergencies can still occur on construction sites. Having comprehensive emergency response and evacuation plans is crucial for minimizing injuries and protecting workers when accidents happen.
These plans should clearly identify emergency exit routes, assembly points, and procedures for different types of emergencies such as fires, structural collapses, or severe weather events. Regular drills ensure all workers know exactly what to do during an emergency without hesitation.
Every worker must know their role during an emergency, including who will conduct head counts and who will liaise with emergency services. Designated first aid stations should be clearly marked and accessible, with trained personnel available on each shift.
Communication systems are vital components of effective emergency plans. Multiple methods of alert should be established, considering the noisy nature of construction environments.
Understanding Construction Site Risks
Construction sites present numerous hazards that can lead to serious injuries and fatalities if not properly identified and managed. Recognizing potential dangers and fostering a strong safety culture are foundational steps in developing effective accident prevention strategies.
Common Hazards and Their Impacts
Falls from heights remain the leading cause of construction fatalities, accounting for roughly 36% of all construction deaths annually. Scaffolding collapses, unprotected edges, and improper ladder use contribute significantly to these statistics.
Struck-by incidents involve workers being hit by moving equipment, falling objects, or vehicles. These accidents account for approximately 10% of construction fatalities.
Electrical hazards present serious risks through exposed wiring, overhead power lines, and faulty tools. Even low-voltage shocks can cause severe injuries or cardiac arrest.
Caught-in/between hazards occur when workers become trapped in machinery or crushed between objects. Trench collapses are particularly dangerous, with mortality rates exceeding 40% in cave-in incidents.
Chemical exposures and respiratory hazards can lead to both acute injuries and long-term health conditions. Silica dust, asbestos, and toxic fumes require proper protective equipment and ventilation controls.
Role of Safety Culture in Accident Prevention
A robust safety culture serves as the foundation for effective risk management on construction sites. When safety becomes a core value rather than just a priority, accident rates typically decrease by 20-40%.
Leadership commitment establishes the tone for site safety. Management must visibly demonstrate that safety takes precedence over production schedules and costs.
Worker involvement in safety planning increases hazard identification by up to 50%. Employees on the front lines often recognize risks that may be overlooked by supervisors.
Regular safety training reinforces proper procedures and keeps hazard awareness fresh. Companies with comprehensive training programs report up to 60% fewer accidents than those with minimal training.
Clear communication channels enable prompt reporting of unsafe conditions. Establishing a non-punitive reporting system encourages workers to identify hazards without fear of reprisal.
Legal and Regulatory Considerations
Construction companies must navigate complex legal frameworks designed to protect workers and ensure safe working environments. Compliance with these regulations not only helps prevent accidents but also shields employers from potential liabilities and penalties.
Relevant Occupational Safety Standards
OSHA (Occupational Safety and Health Administration) regulations form the cornerstone of construction safety requirements in the United States. Employers must comply with standards outlined in 29 CFR 1926 specifically addressing construction safety.
Companies must maintain accurate records of workplace injuries and illnesses using OSHA 300 logs. These documents can be requested during inspections and are critical for legal compliance.
State-level regulations often impose additional requirements beyond federal standards. Construction managers should consult with safety specialists to ensure compliance with all applicable local laws.
Regulatory violations can result in substantial penalties, with fines reaching up to $145,027 per violation for willful or repeated infractions as of 2025.
Digital compliance tools can significantly streamline regulatory adherence. Modern solutions help companies track training certifications, equipment inspections, and incident reports in real-time.
FAQS
Tim Wolter
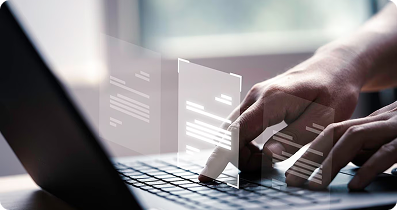